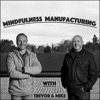
117 You Can’t Proceduralize Everything! With Jake Mazulewicz
Mindfulness Manufacturing
English - May 15, 2024 07:40 - 30 minutes - 22.2 MBManagement Business Education Self-Improvement emotionalintelligence leadershipdevelopment manufacturing Homepage Download Google Podcasts Overcast Castro Pocket Casts RSS feed
When a mistake occurs on the plant floor, your mind might jump to one question: who caused this issue, and should I write them up for their mistake? But there’s a more productive approach you could be taking—and in this episode of Mindfulness Manufacturing, guest Dr. Jake Mazulewicz breaks it all down!
With a background as a firefighter, EMT, and military paratrooper, Jake knows the challenges of high-hazard industries, and works with organizations to reduce errors and create safer, more reliable workplace environments. In this episode, Jake shares why you can’t procedularize everything, including the way you handle errors and accidents, and offers great insights and stories about how to use connection and curiosity to improve safety, address errors, and strengthen your organization.
3:35 – Procedures and policies are the work that is imagined, and on the floor is how the work actually gets done
4:19 – The work as-done is almost always radically different than the work as-imagined
5:20 – Even when you have standards and people show up wanting to do a good job, you can still see issues that need to be addressed
6:44 – There will always be areas that absolutely need to have procedures in place
8:02 – There are also adaptive jobs, which leans less into procedures and more intro troubleshooting and tacit human knowledge
10:56 - In an ideal environment, both mechanistic and adaptive models are used and respected and needed
12:11 – There are four levels, ranging from strict procedurals to looser guidelines that show what to do, but not how to do it
15:36 – Tacit knowledge gets shared through conversations
16:22 – A way to share important information is to have frontline experts record videos sharing their insights to problems, especially those that are not covered in procedures
19:44 – Through conversation and connection, more knowledge is shared
21:58 – Debriefing also plays a central role
23:45 – If you have strong discipline, you’ll find more freedom
25:31 – In most situations, errors are signals, not defects
27:07 – When an error occurs, be curious and find the deeper cause of the problem
Connect with Jake Mazulewicz
Find him on Linkedin
Visit his website