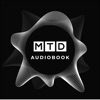
Nov 2019 - 19: ISCAR imparts turning wisdom at seminar
MTD Audiobook
English - November 28, 2019 09:25 - 5 minutes - 8.18 MBBusiness Science mill cnc cutting drilling lathe machining machinist manufacturing metal milling Homepage Download Apple Podcasts Google Podcasts Overcast Castro Pocket Casts RSS feed
ISCAR Imparts Turning Wisdom at Seminar
Last month ISCAR hosted its Machining Techniques Customer Seminar.
The two-day programme welcomed more than 320 customers .
MTD magazine visited the action-packed event to look at the latest innovations.
Following-on from the successful event that the cutting tool manufacturer hosted in June, the comprehensive Autumn programme was packed with cutting tool demonstrations that were transmitted live from the technical centre to the seminar theatre.
The demonstrations covered all core disciplines with H-S-M strategies, continuous and intermittent parting, drilling, turning, titanium milling and much more.
Each of the 30-minute demonstrations were highlighted in a seminar booklet that provided attendees with the cutting data, material grade and performance characteristics of each tool.
The demonstrations included shouldering and slotting with the 16mm diameter MULTI-MASTER solid carbide milling range.
There were numerous examples of the indexable MULTI-MASTER line that included grooving, scanning, corner rounding, pocketing and chamfering – all followed by the SOLIDMILL premium line conducting trochoidal strategies.
Other highlights from the milling stable included the MILL4FEED, LOGIQ4FEED, MICRO3FEED and SOLIDFEEDMILL, which were conducting high-feed roughing, rest machining, pocketing and finishing.
The turning line provided impressive demonstrations from the LOGIQ4TURN, SLIMGRIP, ISOTURN, SUMOCHAM.
Also present was the brand new MULTIFGRIP blade holding tool bodies and the TANGFGRIP high-feed parting-off blades that MTD magazine covered in the September issue.
We spoke to ISCAR Tools, Andy Hayward who talked us through the benefits of the new parting line.
The continuous parting demonstration undertaken on the company’s Ma-zak Quickturn Smart 350 at the event was dry parting a 50mm diameter bar of EN19 at 0.25mm/rev, 0.35mm/rev and 0.5mm/rev.
Andy Hayward says: “We have found that you cannot increase the rigidity of parting systems by making the tool wider, as the insert width restricts the tool holder support in the groove.
You can only improve them from making them deeper and this is what we have done with the new MULTIGRIP and TANGGRIP system.
Standard parting tools run at a feed rate of 0.15mm/rev to 0.2mm/rev on EN19, the MULTIFGRIP tool holder supports the new square block TANGFGRIP blades to minimise vibration and deflection, so cutting feeds can be more than doubled through the new deeper design."
To emphasise this rigidity, the second demo at ISCAR was undertaken on 120mm diameter bar with 60mm tool overhang.
This second demonstration running with 20bar coolant pressure through the ISCAR JETCUT high-pressure coolant system was initially run at 0.25mm per-revolution, then 0.35mm per-revolution and finally 0.45mm per-revolution.
With competitor parting systems typically running at 0.15 to 0.18mm per-revolution, the vibration dampening characteristics of the TANG-F-GRIP and 4-insert MULTI-F-GRIP blade are easily achieving feed rates at between double and even treble that of alternate systems.
Pushing the benefits of the rigidity across to attendees, ISCAR ran the same 50mm and 120mm diameter demonstrations under interrupted cutting conditions.
Applying its new IC808 insert grade that is a general grade for steel, stainless and exotics, the performance characteristics were impressive, running at 0.25, 0.35 and 0.5mm/rev.
Discussing the performance of the MULTIGRIP, Andy Hayward says:
“When running the new parting system at 0.2mm/rev on intermittent cuts, it makes a nice dull sound that highlights how the forces are being absorbed through the tool and into the machine.”
“We have run tests with the new MULTIGRIP on SAE 4140 steel at a speed of 150 meters/min at a feed rate of 0.4mm/rev with a 60mm tool overhang.
Using the old ISCAR parting system with the TGSU353IQ blade, the blade would deflect by 0.325mm when intermittent machining at these parameters.
The new MULTIGRIP deflects by less than 0.169mm, that is a 60% reduction on the previous system.
That is a huge difference and the visitors to our Machining Techniques Customer Seminar were clearly impressed by the huge leap forward ISCAR has taken with this new system.”