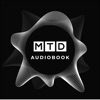
Nov 2019 - 16: Lehmann rotary table provides accurate and flexible machining
MTD Audiobook
English - November 28, 2019 08:51 - 7 minutes - 10.9 MBBusiness Science mill cnc cutting drilling lathe machining machinist manufacturing metal milling Homepage Download Apple Podcasts Google Podcasts Overcast Castro Pocket Casts RSS feed
Specialising in precision engineering and optical systems, Loesch T-P-L Feinwerktechnik was founded in 1950 in Darmstadt.
With a workforce of ten and an annual turnover of €2m Euros, LOESCH T-P-L is a source of ideas as well as a supplier to major machinery manufacturers.
At the company’s production facility, complex parts are machined with impeccable accuracy and the Mazak VCN 530C VMC stands out for its efficiency.
This is credit to the addition of a two-axis C-N-C rotary table from pL LEHMANN that allows the machine to undertake full five-sided machining.
Loesch's product range covers three main areas that includes testing equipment for the automotive industry; handling devices and components for plasma powder and laser cladding and measuring and testing equipment for the pharmaceutical, cosmetics and chemical industry.
Managing Director Michael Loesch says: “We are more than just a metal-cutting service provider.
We are best described as an innovative partner of various renowned enterprises, primarily supplying ideas, developments and our own products.
Our know-how in these areas is extensive, and we not only apply it to the manufacture of parts, but also to their mechatronic requirements.
Of course, metal cutting is a core competence because all complex parts are manufactured in-house.”
The company's ground floor houses six Mazak CNC machines.
“We've had close ties with this manufacturer since 1979.
Back then, my father, the founder of our company, ordered the first Mazak lathe.
Further lathes and machining centres were added over the years, and we have always happily relied on Mazak's technical advice, delivery and customer care.”
The latest addition, a 3-axis VCN 530C VMC has been purchased and its potential has been enhanced by the addition of a C-N-C rotary table combination from pL LEHMANN to facilitate 5-axis machining.
LOESCH T-P-L decided that for efficiency reasons the C-N-C rotary table was the most suitable addition.
Using five-axis milling and drilling technology, Michael Loesch realises benefits for many workpieces from across the entire range of customers.
He says“In general, all parts can be manufactured on a 3-axis machine.
However, this requires special clamping fixtures for angled surfaces and bores.
Additionally, multi-sided machining always requires the re-clamping of parts in different positions.
This costs time and is detrimental to accuracy. From a technical and economic point of view, 5-axis machining is beyond compare.”
The reason for the configuration is because a 5-axis machine was not an option for Michael Loesch:
“Rocker-mounted rotary tables are usually rather small, or we would have had to spend a lot of money for a correspondingly larger machining centre.
For us, the Mazak VCN extended by the Lehmann rotary/tilting table is the perfect solution.
It even leaves enough room to accommodate two more vices on the machine table, thus providing further clamping options for simpler workpieces or the sixth side.”
This type of solution also entails interfering edges that require a raised fixture for the workpiece or at least long tools.
These both reduce stability, promote vibration and ultimately reduce precision and machine performance.
Moreover, a 3+2-axis solution is less expensive while offering greater flexibility.
With the Mazak VCN 530C, Michael Loesch and his team of metal-cutting experts are convinced to have found the most productive vertical machining centre solution.
Cycle times are very short thanks to the high feed rate of 42 m/min, excellent acceleration/deceleration and quick tool changes of just 2.8 s.
Durable linear roller guides ensure consistent machining accuracy along all axes.
The machine was specified with a 40-tool magazine, an 18’000rpm high-speed spindle and a Knoll 70 bar high-pressure coolant system, reducing machining times for deep-hole drilling by up to 90%.
For LOESCH, the 1300 x 550 mm table was of particular importance as it can fit the C-N-C rotary table from pL LEHMANN and still provide enough space for two vices of size 125.
Supported by the rotary table specialists from Switzerland and German sales and service partner IVO Oesterle, the team selected the two-axis model T1 TOP2.
“The Swiss quality won us over at the first presentation. With regard to performance and suitability for digitalization and Industry 4.0, we did not consider any of the alternatives.”
3D-CAD data of the C-N-C rotary table were submitted to the team beforehand, so a matching workspace concept could be worked out in the in-house CAD system.
The two-axis LEHMANN rotary table T1 TOP2 is 711mm long, 301mm wide and 250mm high.
It clamps workpieces of up to 340mm in diameter.
Michael Loesch says “That's more than enough because we mainly process small to medium-sized workpieces at about 150mm".
A torsionally rigid overall system was a key requirement, so the decision was made for a clamped counter-bearing.
He says “Besides copper, brass, aluminium and bearing metals, we often process stainless steels that cannot be roughed without this option.”
To this effect, a clamping torque of 800Nm in the 4th axis and up to 4’000Nm in the 5th axis was a convincing feature.
Also, precision is a core value at LOESCH.
The indexing accuracy solution specified by pL LEHMANN of +/- 17 arc second and +/- 21 arc second (4th and 5th axis) as well as the average repeat accuracy positions of +/- 2 arc second, correspondingly, was verified by the metal-cutting experts on site using a calibration cube.
The result exceeded the specifications. In practice, the high positioning speed of the rotary/tilting table is another great benefit.
Michael Loesch is very satisfied with his investment:
He says “Thanks to the Mazak VCN 530C and the two-axis rotary table from pL LEHMANN, we have achieved significant time savings and reduced the effort required for re-clamping, thereby freeing up our machine operators to take care of other tasks.”