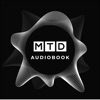
Jan 2020 - 16: How Guhring and Chiron are together milling their way
MTD Audiobook
English - January 29, 2020 17:00 - 7 minutes - 16.6 MBBusiness Science mill cnc cutting drilling lathe machining machinist manufacturing metal milling Homepage Download Apple Podcasts Google Podcasts Overcast Castro Pocket Casts RSS feed
How Gühring and Chiron are together milling their way into the HPC record books
As machine manufacturer and cutting tool specialist, Chiron and Gühring share common development goals and the aspirations.
Both aim to deliver outstanding products and to further increase their respective efficiency through symbiosis.
Together, the Swabian manufacturers have now set a ground-breaking record: machining 1,000cm3 of steel in 60 seconds.
That’s eight kilograms of steel per minute!
Common development goal
With an extreme metal removal volume and a massive feed rate, both companies were pursuing the same goal, namely launching a product that excels in both dynamics and performance.
The companies both had a new product in development at the same time – Chiron had the new FZ16 five-axis and Gühring had a variant of the Speed Ratio milling cutter.
Thanks to many years of cooperation in the project business, Gühring and Chiron are always in close contact and sharing ideas. It was only in the summer that they carried out joint initial tests with prototypes.
Once both products, the Ratio milling cutter and the 5-axis machining centre, were market-ready, the experts came together to prove their performance under real conditions.
Milling specialist Rolf Ehrler from Gühring says “Due to the ever-increasing performance requirements of our customers, we jointly devised the idea for a record attempt, and the result was an incredible 1,000cm3 of steel per minute”.
The interplay of machine dynamics and milling stability is what makes such high metal removal rates possible and is bound to set pulses racing in the mould making, aerospace and automotive industries.
Two products, one aspiration: top performance
The Gühring RF 100 Speed P tool is a roughing cutter specially adapted for machining steel, high-tensile steel and cast iron.
Its 48° helix angle with unequal cutting-edge partitioning ensures a soft, quiet cut and great running smoothness.
This reduces the load on the machine and increases the volume performance.
The optimised chip gullet with a deep flute in the front cutting-edge area, ensures improved chip evacuation when ramping and helical plunging. This allows swarf to be transported reliably out of the machine.
Thanks to a corner protection chamfer and face correction, a stable cutting-edge corner was ensured.
Chip breakers and the extreme cutting-edge length on the milling tool ensure a soft cut and great running smoothness.
This reduces the load on the machine and increases the volume performance. This all culminates to provide perfect conditions for the FZ16S five-axis single-spindle machine from Chiron.
This machining centre is designed for the particular demands of accuracy when it comes to 5-axis machining.
At the same time, it really stands out with its optimum dynamics, ensuring high productivity.
The right tool is essential here. Michael Eble is Head of Machine Development at Chiron.
He says: “We have significantly increased the drive power as well as the dynamics and cutting performance of the 16 series.
But the real fun begins when the tool manufacturer is then obliged to deliver an even more efficient tool because the machine can do even more.
That’s when you know you’ve done things right.”
Milling strategy: HPC roughing
The specialists at Gühring applied the modern HPC strategy.
Controlling the cutter path with low radial feed that allows for comparatively gentle edging of the workpiece.
HPC roughing is ideal for machining large cutting depths, as the roughing cutter machines the entire depth of the workpiece with the whole length of the cutting edge.
The cutting forces are reduced and evenly distributed over the entire length of the cutting edge.
This allows for high processing speeds and long service lives.
High-performance cutting is the first choice for applications with enormous material removal rates.
The components to be machined are usually made of high-tensile steels, which place increased demands on the machining process.
In order to achieve appropriate results, higher cutting speeds, higher feed rates per tooth and greater cutting depths are used.
The high cutting speeds are achieved with the help of high revolution frequencies, as long as the milling machine allows for this.
By using the entire length, the load placed on the cutting edges of the milling cutter at the perimeter is significantly less and wear is reduced. The milling process isn't new, but the basis of the performance of today’s machining centres such as the FZ16S five-axis, geometry adjustments and the wear resistance of milling tools, that HPC reveals itself as an advancement in machining when it comes to enormous metal removal rates.
The major goal was to set a benchmark in this respect, while ensuring absolute process reliability.
Rolf Ehrler says “Thanks to the 48° helix angle, we can create an extremely soft cut.
This means that the tool literally peels the chip out. And the best part is the great running smoothness, which protects the machine.” This was also recorded and verified by appropriate vibration analyses – integrated in the machine.
This vibration analyses and the dynamics of the machine combined with the efficient Ratio milling cutter and the HPC milling strategy guarantee process stability and therefore more parts with the highest precision.
Unprecedented cutting parameters
Under HPC conditions, the entire length of the cutting edge is used with a small cutting width, just 5-15% radial engagement (otherwise known as 'width of cut').
This allows for incredibly high feed rates.
The feed per tooth was 0.5mm during the record attempt.
With four teeth, this means two millimetres feed per revolution.
This is of interest to all companies that have large quantities of steel to cut.
This includes machine components, and the classic tool and mould-making industry, where mainly high-tensile steels are found.
Primarily, though it's in aerospace, where lightweight components made of solid material with a material removal rate of up to 96% are produced.
Of course, the special cutting-edge geometry can also be used optimally in the automotive and supplier industries and is very popular due to the large cutting-edge length.
Michael Eble from Chiron is satisfied, he says: “We have succeeded in significantly increasing the milling stability and dynamics of a new machine series.
In conjunction with the new Gühring RF 100 Speed P milling cutters, things are possible which have never before been achieved.”