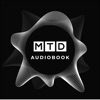
Jan 2020 - 11: When Precision Creates Joy
MTD Audiobook
English - January 29, 2020 17:00 - 3 minutes - 8.94 MBBusiness Science mill cnc cutting drilling lathe machining machinist manufacturing metal milling Homepage Download Apple Podcasts Google Podcasts Overcast Castro Pocket Casts RSS feed
When Precision Creates Joy.
The headline phrase isn’t commonly associated with mechanically engineered parts, but it sums up how one company owner views his production facility.
Werner Buschorr owns a medium subcontract manufacturing plant in Switzerland and had two growing problems.
The first was that his customers’ tolerances were getting tighter and on his existing equipment he was relying on his operators to ‘tweak’ the programmes and tooling to achieve the desired results.
His second issue was that his production was reliant on his operators, and as customer delivery times were becoming shorter, he had to look at production when the machines were not attended in the evenings and at weekends.
Founded in 1989, Buschorr Praezisionsmechanik AG is always looking for real precision in the parts they manufacture, which included prototype batches with as few as 20 components up to production runs of 20,000+ parts.
This huge range in the quantity of components produced by the Swiss company, tested the efficiency of the company.
When trying to find answers to his accuracy problem Werner Buschorr found KERN Microtechnik and was soon able to realise that the KERN Micro machine was also able to help solve his second problem of working unmanned.
He says: “The KERN Micro is the first milling centre that can stand up to our measuring machine, which we purchased two years ago.
The measuring machine has a measurement uncertainty of half a thousandth of a millimeter and the Kern Micro offers a positioning accuracy of half a thousandth of a millimeter.
The first KERN Micro was immediately connected to a System 3R automation system, with the possibility of adding another machine.
The large tool magazine with 186 tools and the repeatability of the KERN Micro are ideal for automatic production.
Finally, we can manufacture workpieces that require the highest level of unmanned precision.”
Key to this solution is the thermal stability of the machine with its smart cooling management system that ensures the temperature of the structural components of the machine remains constant with a maximum deviation of 0.2 oC.
For KERN, the performance of the patented light-metal axis structure and software for volumetric compensation bring the performance of this high-tech machine to an unmatched level.
In terms of 5-axis machines, the consistency of achieving tight tolerances on all faces was paramount, so it was important that the swivel position of the table was at the base of the component.
The flexibility of the tool magazine was also important.
The tools are held on pallets that are easily loaded and unloaded from the magazine, giving flexibility to store a particular set of tools away from the machine till the next batch comes along.
A tool pallet can hold the sensitive tools for a particular job, while standard tools would be set up on a different pallet.
Another advantage is the compact design of the KERN.
The 4m2 footprint surprised Buschor with the amount of accessibility that the machine provided for the tool magazine.
As with most companies, producing a first-off component is normally difficult.
To ensure everything was within tolerance, a part would be manufactured, measured, tweaked, then the procedure was possibly repeated.
On the new KERN, Buschor says the first part fits the drawing specification and this saves a lot of time and effort.
To improve matters, a second KERN Micro has been installed and connected to the workpiece changer, giving Buschor a powerful unmanned cell.