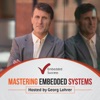
Muda, Mura and Muri – Waste in SW-development – MES024
Mastering Embedded Systems
English - December 15, 2015 07:15 - 11.2 MB - ★★★★★ - 4 ratingsBusiness Technology Homepage Download Apple Podcasts Google Podcasts Overcast Castro Pocket Casts RSS feed
I have recorded this episode twice. Not by intention - far away from that. But I was neither convinced nor satisfied with the first recording. Also the subject was not really impressive and I decided to do it again from scratch. Thus I got a first hand impression what waste of time and effort is. However one detail in the first record was amazing. It was about waste in SW-development.
You remember episode 4? Already there I have mentioned waste due to over-processing and over-engineering. Both are part of the 7 forms of regular waste in any kind of system.
The Toyota Production System (TPS) has introduced to a broader audience the classification of waste forms. In this episode I wanted to connect traditional manufacturing based Kaizen and Muda, Mura, and Muri with Software-development. Is it possible? Do we have parallels? Or is the TPS not adaptable to nowadays IT-based technology?
Stay with me and enjoy the show.
I have recorded this episode twice. Not by intention – far away from that. But I was neither convinced nor satisfied with the first recording. Also the subject was not really impressive and I decided to do it again from scratch. Thus I got a first hand impression what waste of time and effort is. However one detail in the first record was amazing. It was about waste in SW-development.
You remember episode 4? Already there I have mentioned waste due to over-processing and over-engineering. Both are part of the 7 forms of regular waste in any kind of system.
The Toyota Production System (TPS) has introduced to a broader audience the classification of waste forms. In this episode I wanted to connect traditional manufacturing based Kaizen and Muda, Mura, and Muri with Software-development. Is it possible? Do we have parallels? Or is the TPS not adaptable to nowadays IT-based technology?
Stay with me and enjoy the show.
Essential Answers Provided In This Episode For:
What is Kaizen?
Kaizen is Japanese and means Improvement. It is regularly used in conjunction with Continuous Improvement. However that’s not the original intention. Kaizen stands for the understanding and the wish that everything can be improved.
Why are there different kind of wastes?
The classification of wastes for manufacturing and assembly purpose is one of the key-concepts in the Toyota Production System (TPS) as one of the three types of deviation from optimal allocation of resources (muda, mura, muri).[2]. Waste reduction is an effective way to increase profitability.
What does Muda stand for?
Lean and TPS knows the key step to distinguish between manufacturing steps which add value and which don’t. The classification of all processes involved into these two categories let one improve the one and eliminate the other. That means Muda is any activity or process which does not add value. Thus it is a physical waste of time, effort, resources and finally money.
Which forms of waste does Muda indicate?
Transport; the movement of product between operations, and locations.
Inventory; the work in progress (WIP) and stocks of finished goods and raw materials that a company holds.
Motion; the physical movement of a person or machine whilst conducting an operation.
Waiting; the act of waiting for a machine to finish, for product to arrive, or any other cause.
Over-Production; Over producing product beyond what the customer has ordered.
Over-Processing; conducting operations beyond those that customer requires.
Defects; product rejects and rework within your processes.
Which forms of waste cannot be adapted to SW-development?
In principle can all forms of waste in Muda be used for SW-development, too. However some of them are quite seldom and do not effectively match always, like Transport or Motion. However others, like Over-Production, Over-Processing and of course Defects seem like exclusively made for SW-development.
What does Mura and Muri stand for?
Mura and Muri define some more abstract ways how waste can be finally created in Muda-categories. Mura and Muri drive Muda.
Mura stands for the waste of unevenness. If the available men, material and equipment are used in a non-balanced way, this finally will result in waste. For example, four weeks ahead of an upcoming milestone the previous measured way of working is changed into a more hectic, confuse and challenging action. The probability of waste, especially defects, will increase. This can be prevented by steering the utilization of all resources in a balanced way.
Muri stands for the waste of overburden. If there is unnecessary stress given on employees and processes this will cause Mura and then Muda. Permanent overburden will cause absences of employees, increase of sickness-rate and finally a higher attrition rate.
Selected Links and Resources From This Episode
Kaizen
Muda
The 7 wastes of Muda
Muda – Mura – Muri
[saf feature="email" cta="Send me feedback"][saf feature="twitter" cta="Reply on Twitter"]
Thank You For Listening
Out of all the podcasts available in the Internet you tuned into mine, and I’m grateful for that. If you enjoyed the episode, please share it by using the social media buttons you see at the bottom of this note.
Also, I would be very happy if you would consider taking the minute it takes to leave an honest review or rating for the podcast on iTunes or Stitcher. They’re extremely helpful when it comes to the ranking of the podcast. For sure I read every single one of them personally!
Or, if you prefer a more direct contact, don't hesitate and drop me a note at [email protected]
The post Muda, Mura and Muri – Waste in SW-development – MES024 appeared first on Embedded Success.