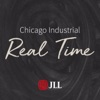
Episode 30: Warehouse Design
JLL Chicago Industrial Real Time
English - February 24, 2020 16:10 - 34 minutes - 27.9 MB - ★★★★★ - 11 ratingsBusiness chicago commercialrealestate industrial Homepage Download Apple Podcasts Google Podcasts Overcast Castro Pocket Casts RSS feed
We’re back with episode 30 and another segment of our industrial education series. Today, you’ll hear from JLL’s Managing Director of Supply Chain & Logistics Solutions, Bob Silverman, who supports JLL’s Northeast industrial group. We discuss rules of thumb and important considerations for both occupiers and developers when choosing an existing warehouse or designing and constructing a new warehouse facility. You’ll also learn about cubic capacity, best-in-class property features, how things flow “inside the box” and how to analyze efficiency.
4:30: Outbound transportation tends to be more expensive than inbound transportation and being close to the customer is critical.
6:39: Some users may benefit from modern, higher clear height facilities by gaining an extra pallet storage position.
11:54: The number of inventory “turns” varies by industry and can help determine an optimal building.
15:39: Tenants are balancing different types of space requirements to determine storage capacity to hold product and the “throughput” requirements to receive and ship volumes.
17:43: In many cases, 36-foot and 40-foot clear are not being utilized, but capital markets considerations and future re-tenanting of the building are spurring the construction of higher cube buildings.
19:33: Site coverage standards are changing dramatically to focus on incorporating more flexible parking layouts.
22:54: Industrial power requirements are increasing as industrial users are requesting greater electric capacities for faster lift truck charging, air conditioning and powering the material handling equipment.
27:32: “Co-bots” is a term used to describe robots and people working side-by-side.
32:29: Autonomous yard spotters may be adopted more quickly than fully autonomous tractor trailers due to their operation on private property.