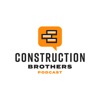
The 2x4 of the Future (feat. John Fay)
Construction Brothers
English - April 26, 2023 04:00 - 39 minutes - 36.3 MB - ★★★★★ - 70 ratingsEntrepreneurship Business Homepage Download Apple Podcasts Google Podcasts Overcast Castro Pocket Casts RSS feed
Today’s episode includes a visual demonstration, so you may want to consider watching the Youtube version. After a short story about deadly dumpling shenanigans, we shift to today’s guest, John Fay. John is the founder and CEO of Låda Cube (pronounced Lauda Cube). Låda Cube produces pre-fab cassettes that are used in the place of conventional stud-and-drywall walls. John starts out with a review of how the cassettes function and the benefits they offer. The refinement of production efficiencies has enabled Låda Cube to explore the benefits of standardization. This standardization yields multiple benefits: Final assembly is more consistent.Assembly can be handled by minimally skilled workersEntire walls can be disassembled and their parts reused–either when it’s time to reconfigure a space or in the case of a more complete demolition. Låda Cube modules are small enough to be easily handled, and they fit together with a cam-lock system that each has 750 lbs of carrying power. The cassette-built wall can then be covered with a variety of finish surfaces that can be switched out when it’s time for a change of decor. John explains that specialized cassettes can serve customized purposes: Increased load-bearing capacityPlug-and-play electrical systemsSpace for plumbing access The goal is to have a system that never goes obsolete–that will be reverse compatible long into the future. John shares about one of Låda Cube’s large recent projects, a series of WalMart vision centers. If the work on these centers would have been done using conventional methods, it would have taken 16 days per center. With the modules, each center was finished in 3 days. We explore the topic of cost. As you might expect, this type of product is currently a premium product. Låda Cube is currently priced at $4.50/linear foot. John believes digitization and production improvements will eventually bring that number below $2. The trickle-down benefits of standardization include faster estimates and reduced errors. John said his crew can generally give a phase-one drawing within just a few hours. The Låda Cube team is now working on software integrations that will populate modules in the design phase so that estimates and invoices can be almost immediate and also transparent. We discuss both cost and quality. John explains that the ½” MDF that is their current main skin finish material. He says that they’re occasionally using Avonite and, in the long run, would like to pursue partnerships with gypsum manufacturers to integrate small panels with easy seam solutions. Tyler asks John to share some of the specific costs related to the Walmart vision center projects, including a large refund that the accountants struggled to process. John anticipates the development of a third-party market for exchanging components of this sort of system. He explains that there is no reason for any of their products to ever end up in a landfill. We hear about door integration when John explains that representatives from MillerKnoll contacted them to say that they’ve never hung a door on a truer wall. This is due to the fact that the Låda Cube cassettes are built to tolerances of 15/100”. Eddie addresses some of the mindset shifts that owners, contractors, and municipalities will need to consider in transitioning to this sort of construction. John’s Megaphone Message: The Låda Cube team sees themselves as changers of environments. When they approach a worksite, they try to remove the fear and tension that might be there. They want to show compassion and to champion people well.
Find John Online: LinkedIn - Låda Cube Find Us Online: BrosPodcast.com - LinkedIn - Youtube - Instagram - Facebook - Eddie's LinkedIn - Tyler's LinkedIn If you enjoy the podcast, please rate us on Apple Podcasts or wherever you listen to us! Thanks for listening!See omnystudio.com/listener for privacy information.